Ansys Crack Propagation Code
Google Translate Api V2. Fracture Mechanics Tools in ANSYS Mechanical Designing structural components to avoid fracture is essential. In 1983, the National Bureau of Standards estimated that the annual cost of structural failure due to fracture was $119 billion dollars. Other costs, such as loss of life, personal injury, and damaged reputations were unmeasured, but obviously could be devastating to individuals, companies, and maybe entire industries. Structures have flaws. They may be large, visible cracks or almost undetectable micro-cracks. They can be inherent in defective material, introduced during the manufacturing process, or created by environmental conditions during operation. Regardless of their source or type, flaws reduce structural integrity.
However, traditional structural design concepts use a strength-of-material approach, which assumes a pristine, flaw-free material. Killwhitneydead So Pretty So Plastic Rar more. To avoid potential catastrophic failure, the effect of flaws must be assessed. Fracture mechanics uses concepts from applied mechanics and material science to assess structural integrity. It considers the combined effect of applied stress; location, size, and shape of cracks; and the resistance of the material to crack growth. Command Line Print Pdf Duplex. CAE is becoming an increasingly important tool in fracture mechanics evaluations. ANSYS Mechanical offers a broad range of fracture mechanics tools, including the capability to calculate traditional fracture mechanics quantities (stress intensity factors, J-integral, and energy release rates), automatically create efficient meshes, and simulate interface delamination.

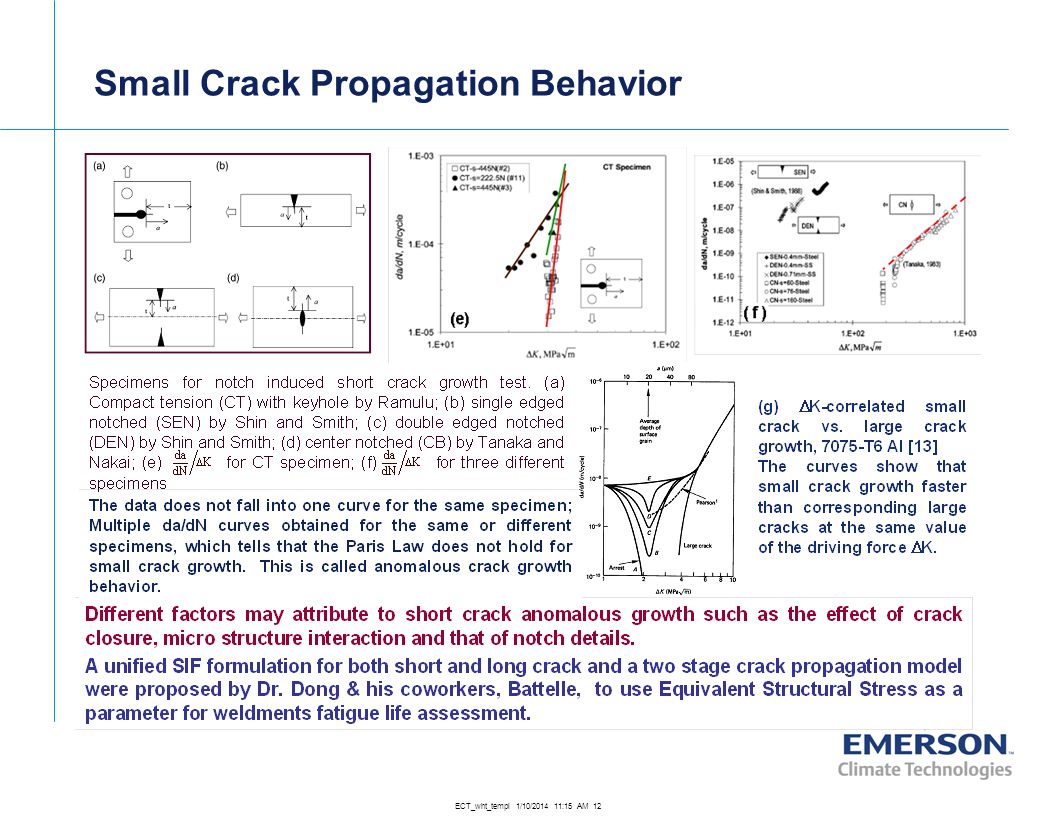
Comments are closed.